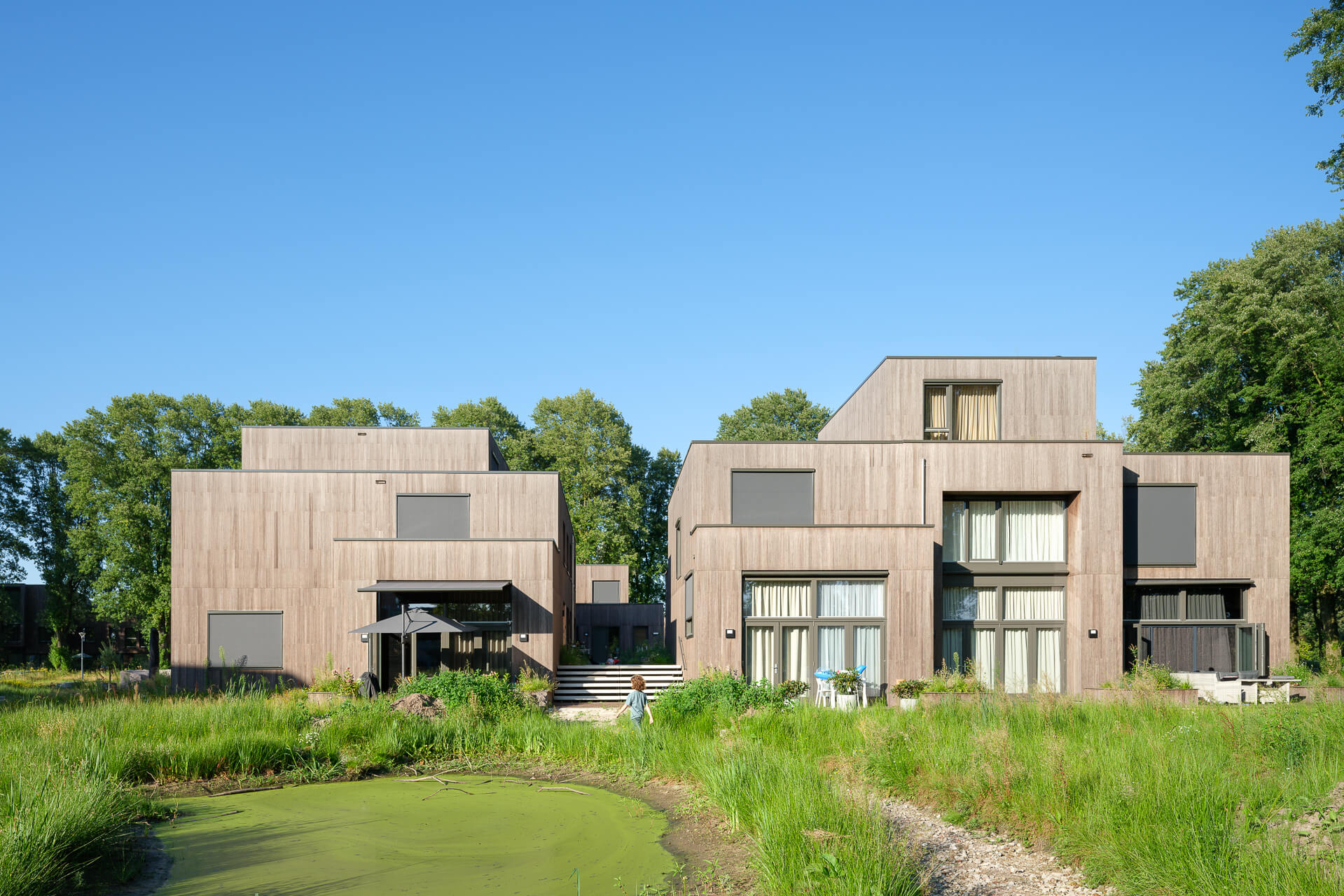
Update: Discover the Finalized Design here 6>
Zuiver Bosrijk: Timber revolution in Eindhoven
Conceived as a circular ecosystem, Zuiver Bosrijk proposes a radical alternative to a conventional Dutch residential neighbourhood. Located in green surrounds on the outskirts of Eindhoven, Zuiver – meaning pure in Dutch – builds a natural living environment on a 1.2-ha site for a sustainable community. The 32 unique residences are designed with freedom in mind. The project follows the highest standards for circular building, centring on closed energy and water systems, upcycled/recycled materials and strengthening biodiversity.
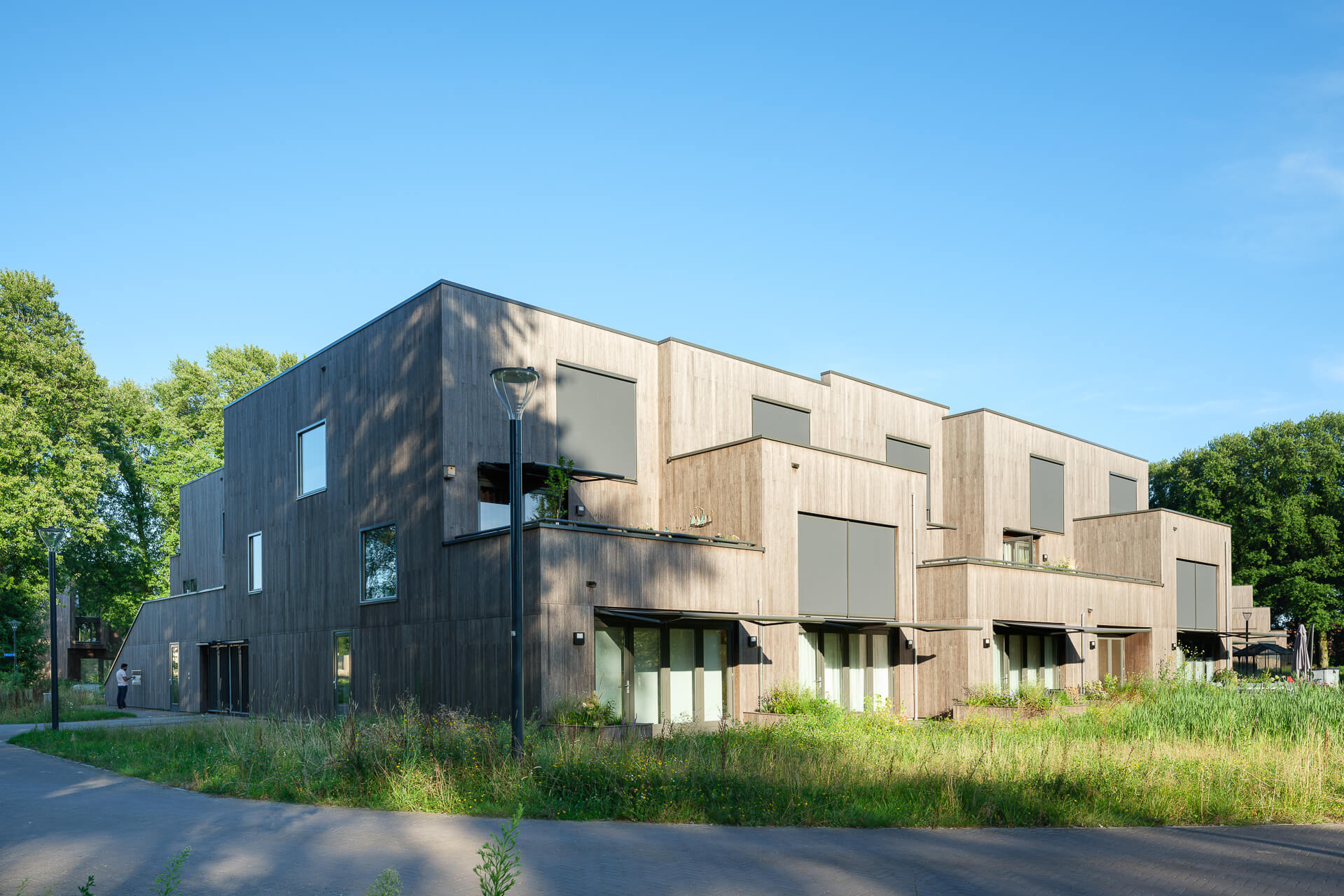
In the Embrace of Trees
Bosrijk is centrally located in Meerhoven and is surrounded by mature trees and greenery. “The location feels a bit like a clearing in the forest,” says developer Joost Katoen of BPD. “The three buildings have been positioned towards the edges, creating a public, shared landscape in the center. The wooden residential buildings, with their terraced design, feel very sculptural, like pieces of art in a sculpture garden. They really stand out in the landscape, but thanks to the open structure of the facades, the connection between the interior and exterior is of exceptionally high quality. You truly live within the landscape here. That is what makes this place unique, especially in combination with the wooden design.”
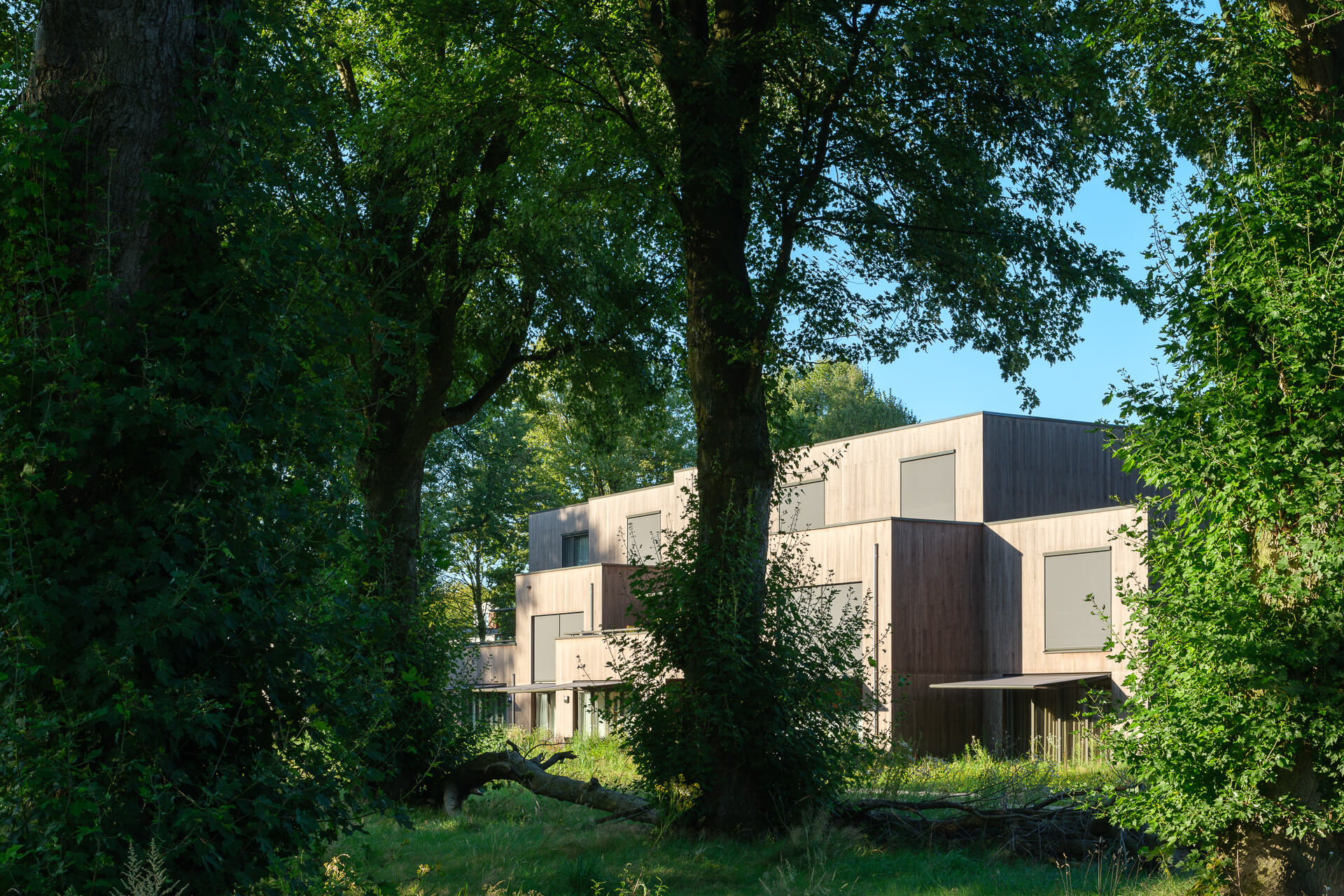
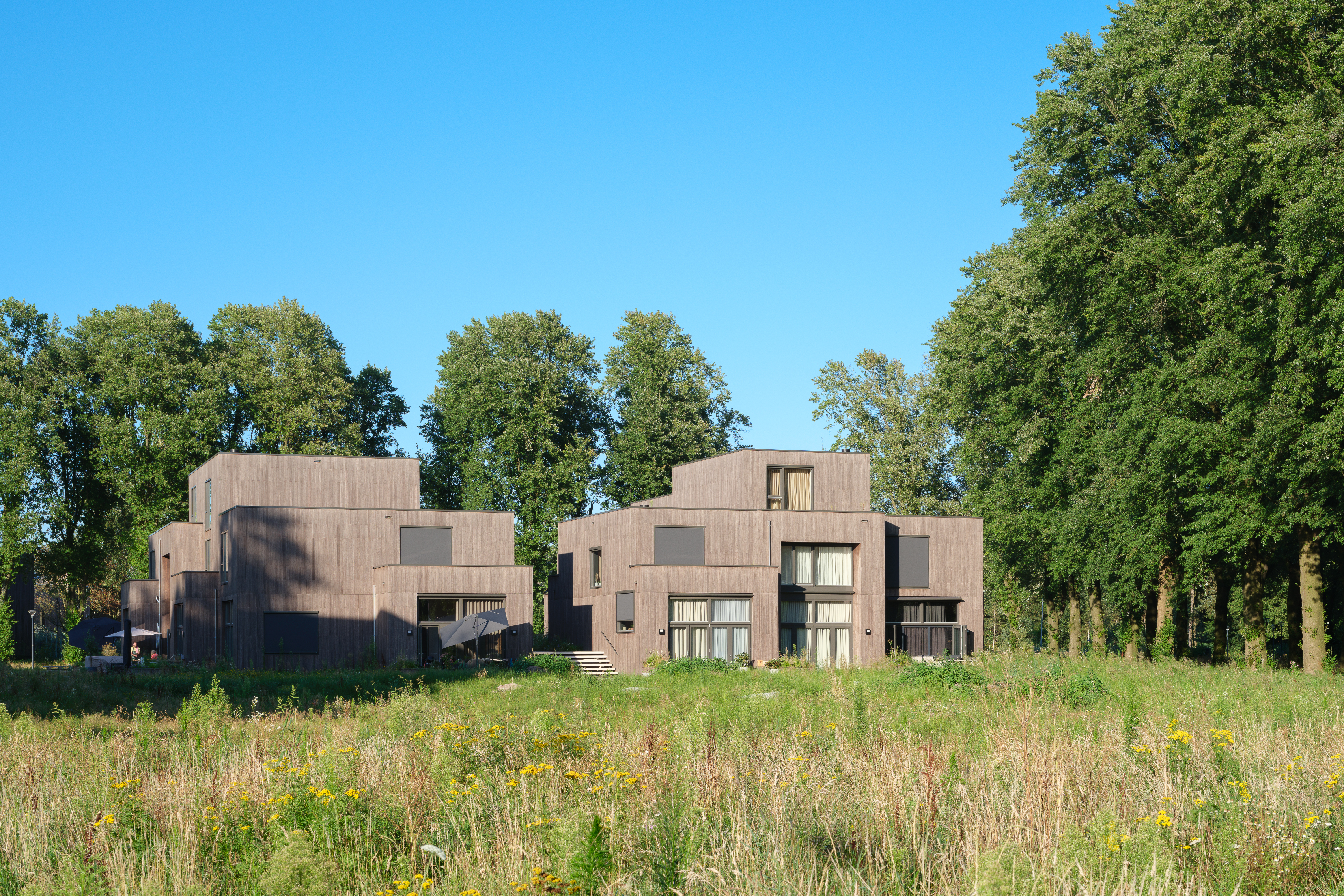
“You can only achieve that connection, according to architect Mai Henriksen, by working with large glass facades that can be fully opened on the ground floor. ‘We played with the volumes, created recesses in the stepped facades, and carefully considered the spatial connection with the outdoors in relation to daylight entry. This way, every home has its own character. People can say, “I live there, that’s my home.” For instance, one home has a huge mezzanine, while another has a living kitchen with a view of the landscape.
Bosrijk follows the design principles of John Habraken: Open Building. Building for the future, with transformable layouts that can adapt to the wishes of the user. The free layout and flexibility, in combination with timber construction, was a tough new challenge for me as a designer. Six-meter spans are the maximum you can do without making thick floors or adding extra support. Look for yourself, this is fantastic! It feels overwhelming. We stuck to this approach throughout the entire design phase.’
Bio-based building means building with renewable natural material sources, so you don’t pollute the planet. In this case, it’s about certified softwood with FSC certification from European forests. By working with dry connections between building elements — MKA’s vision of open building systems — the buildings become demountable and “remountable,” and the building elements can have a second life in the circular economy. This cannot be done with poured concrete. Timber construction, therefore, has a future.”
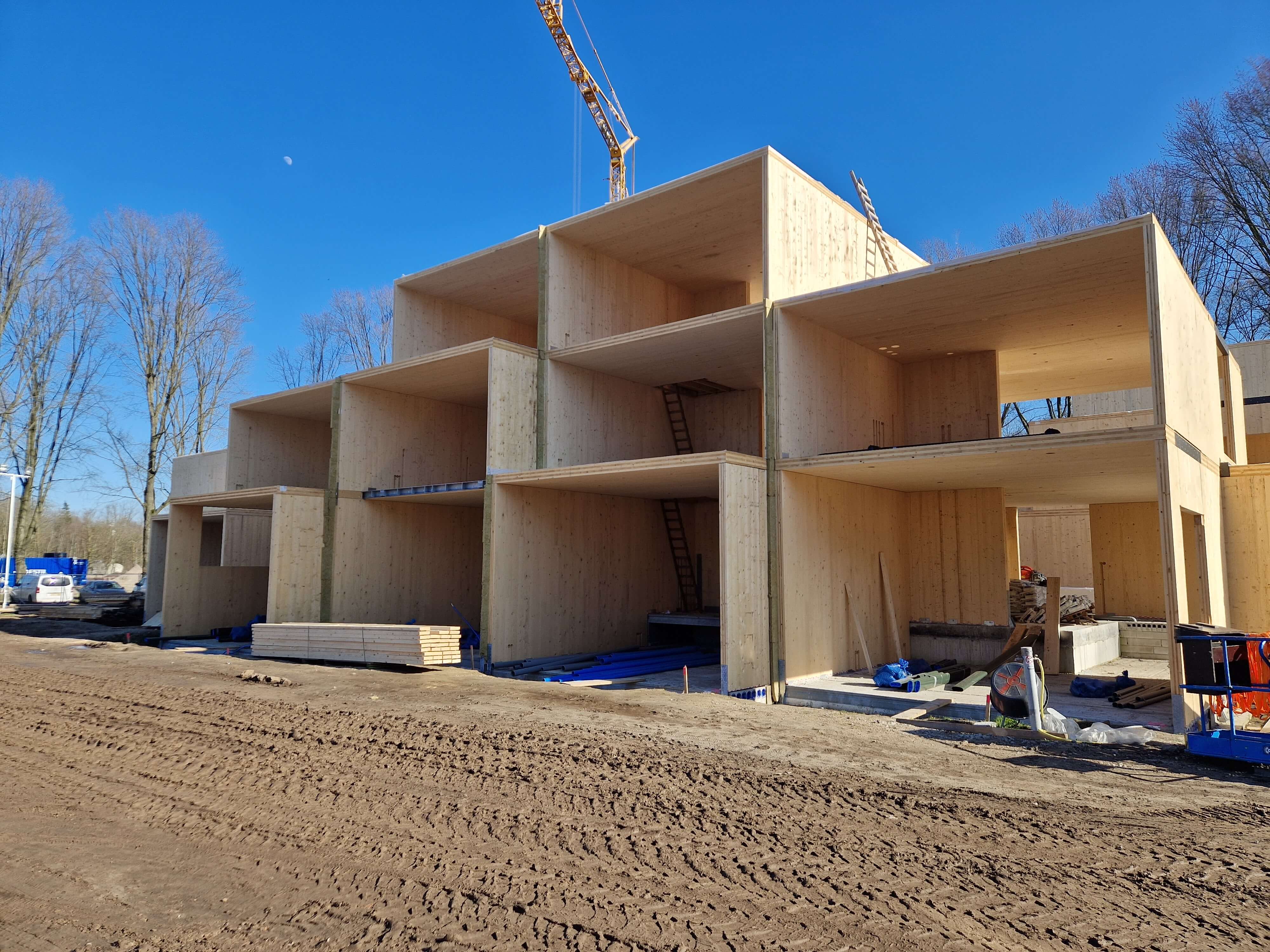
High Sustainability Ambitions
Zuiver Bosrijk is the result of a winning tender issued by the municipality of Eindhoven in 2018. For the team, it was quite logical that wood would be the building material of choice. Mai clearly remembers the brief: “The municipality’s sustainability ambition was sky-high. We quickly agreed that timber construction was a must to achieve the desired quality. Wood is one of the most sustainable materials to build with. Working with natural materials creates a healthy living environment with a healthy indoor climate, which in turn promotes a healthy lifestyle. The fact that the homes were ultimately designed in three separate clusters was a decision we made as a team. Together with BPD, BOOM Landscape, Tom van Tuijn Urban planning, Arcon, Awood and Arup we believed that this design was the best response to key societal challenges such as water retention, heat stress, CO2 reduction, biodiversity, sustainability, social cohesion, and energy.
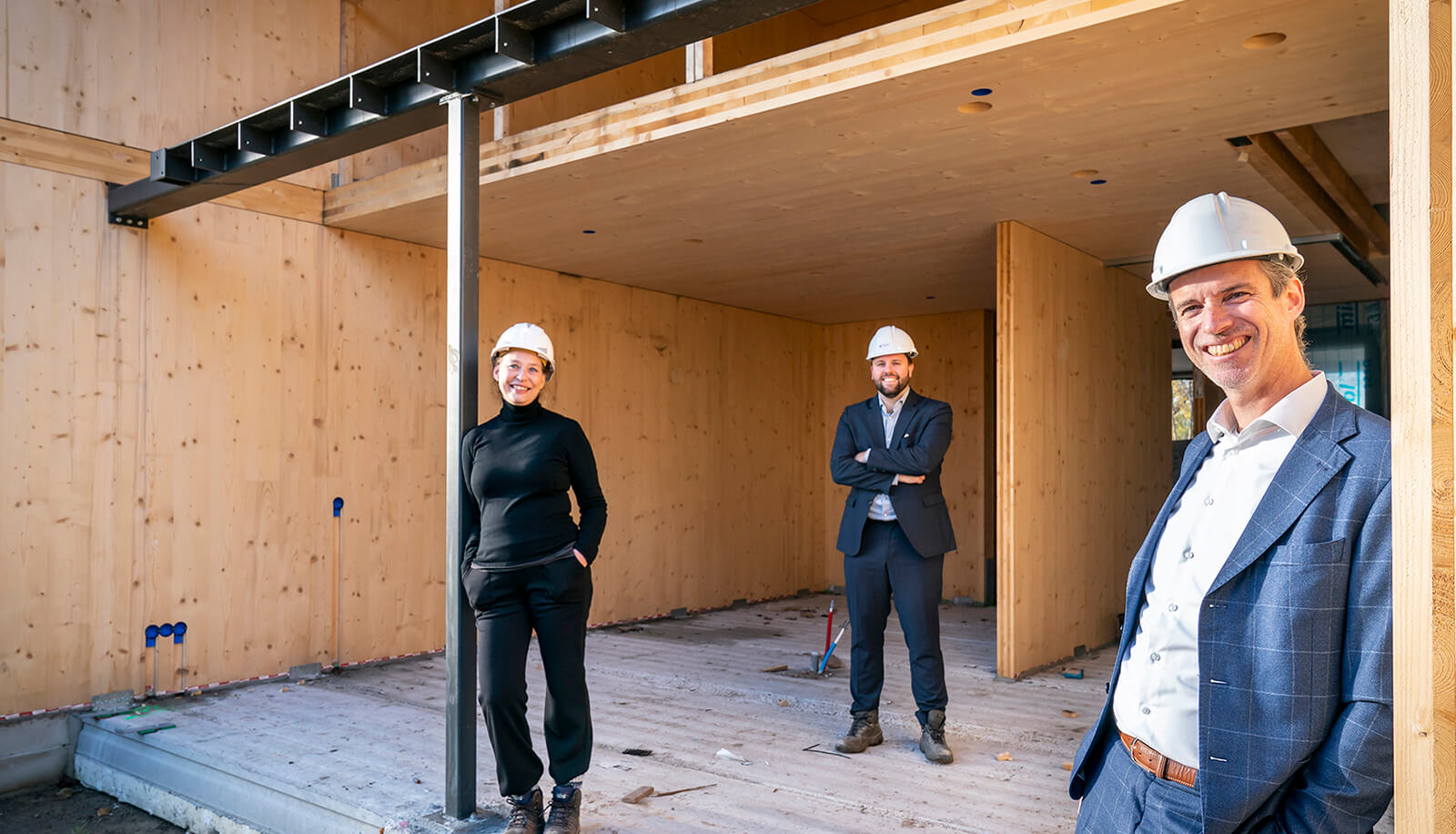
CLT as a healty building material
“Wood is a natural, tactile material. Wood gives a very different feeling than stone,” says sales manager Ruud Beurskens of BPD. “Wood is warmer and feels softer. You have the urge to run your hand over the smooth wood. It looks very inviting. You can even smell the wood when you stand inside the house. It’s a breathable material, which makes it moisture-regulating. The result is a very pleasant home in a very pleasant location.”
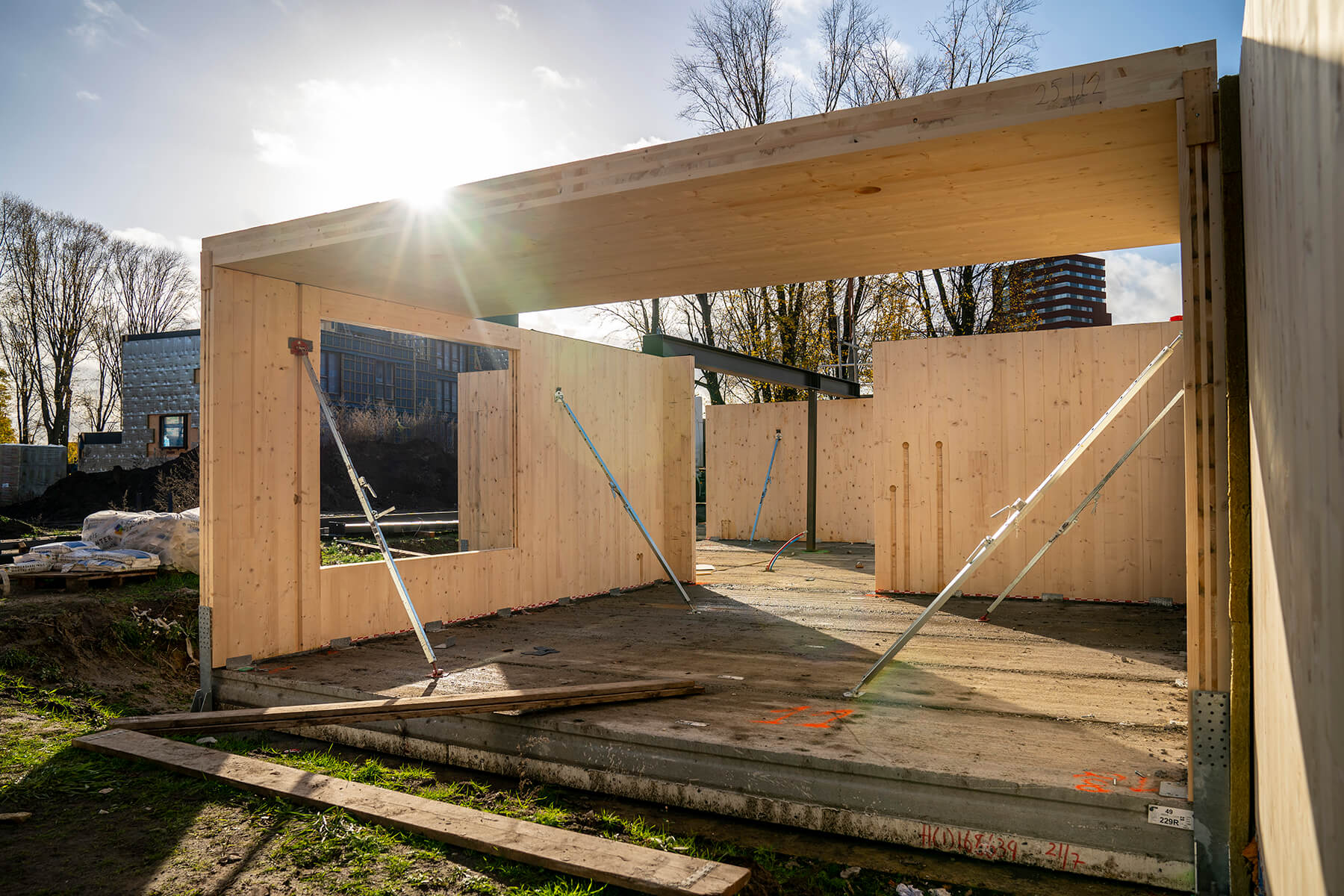
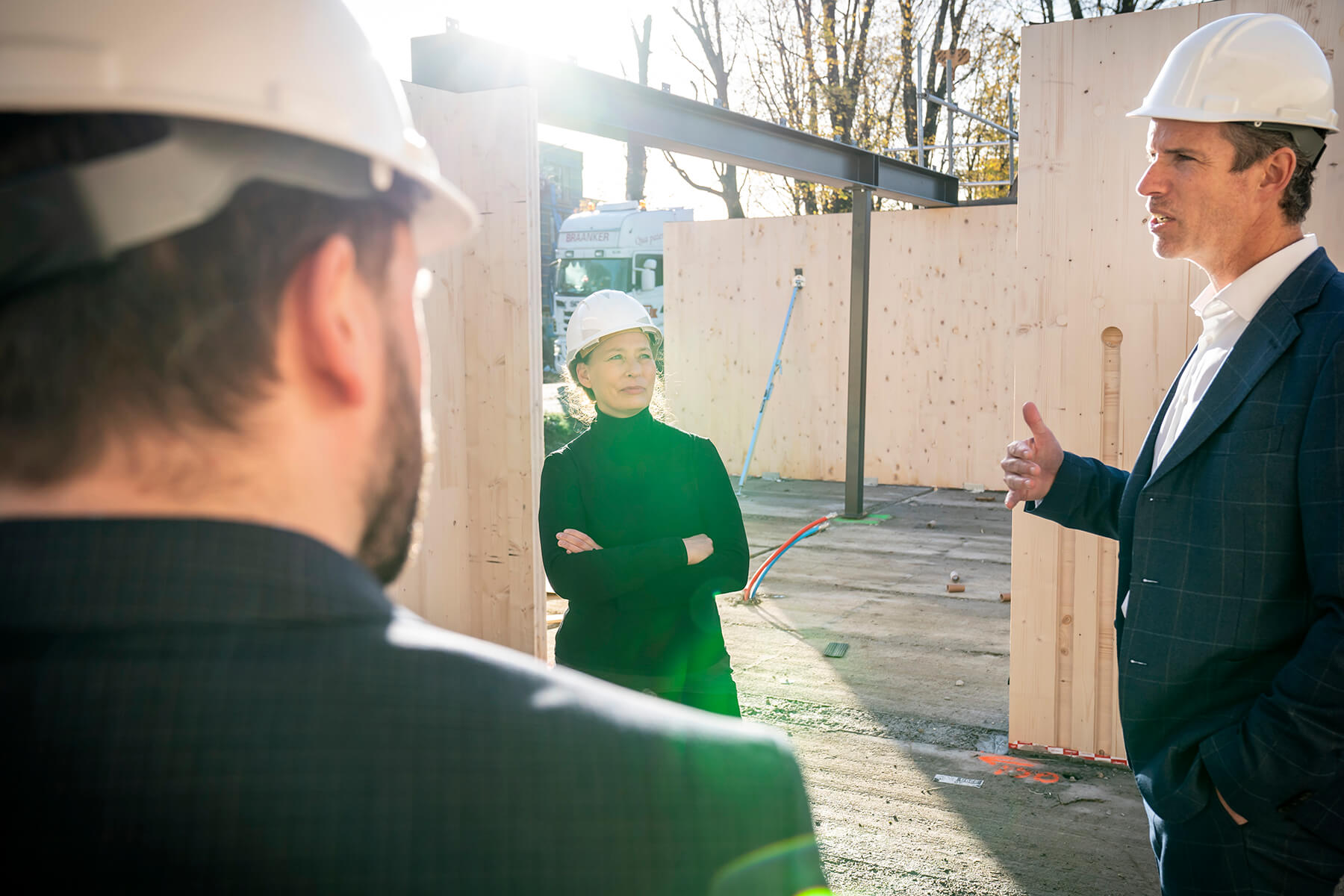
“When you build with wood, you need to include the entire structure,” argues Joost. “At the time, we were one of the first in the Netherlands to do this in a project-based way and with such high-quality architecture. Of course, there were individual self-builders who had done this before, but in this design, you have homes connected both side by side and stacked on top of each other. That naturally presents challenges in the design process. MKA succeeded in developing the homes in such a way that we could maintain the same look as in the tender. MKA has always adhered to all-around quality. For that, wooden tunnels were designed. From there, careful consideration was given to how large facade openings could be created on all sides. This allows for plenty of daylight, and residents can enjoy views of the surroundings from every part of the home.”
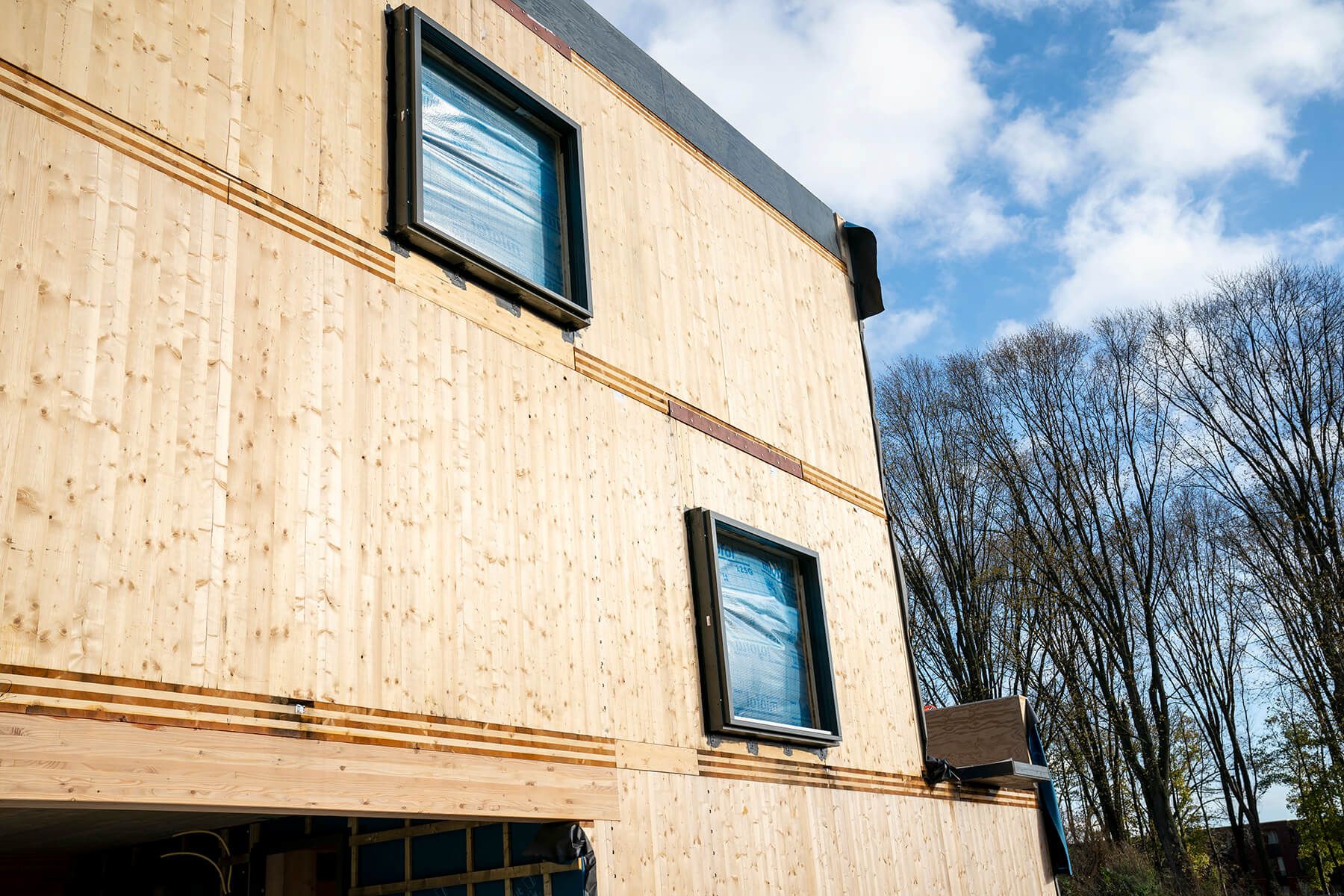
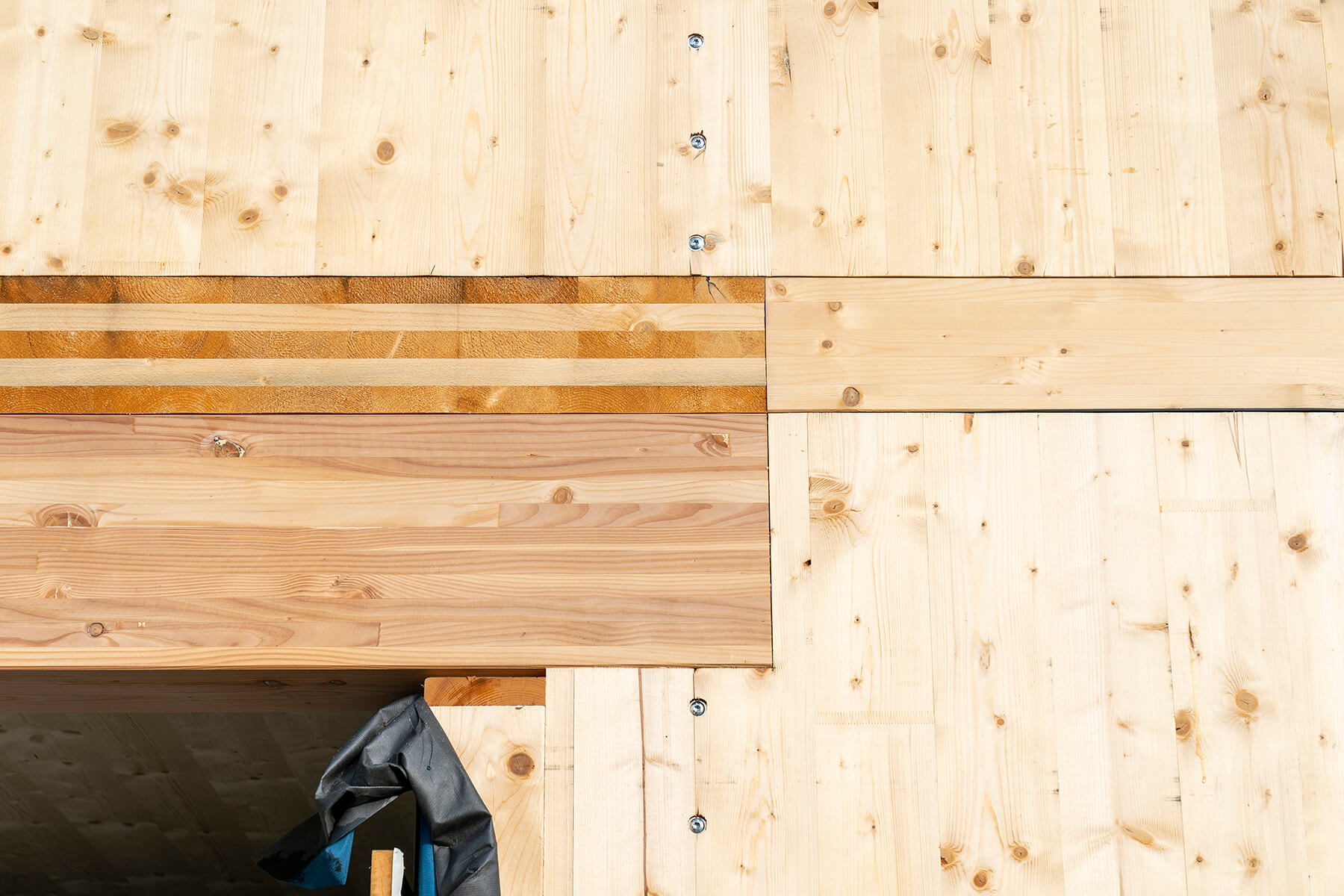
Prefab building kit
“What differs from the wooden materialisation is the underground parking garage. ‘This is made of concrete,’ says Ruud. ‘There’s almost no other option. It creates a solid foundation. Furthermore, all structural walls and floors are made of Cross Laminated Timber (CLT). The great thing is that the finished CLT walls are visible throughout the house. Residents can see what the structure is and which interior walls are made of timber frame construction. The fact that the stability walls are made of CLT affects the layout of the home. You can’t span endlessly with CLT and just be done with it. For example, the gable walls are more closed. In the direction of the landscape and the inner garden, we use timber frame construction and large windows to keep it as open as possible. We learned a lot from these large facade openings. MKA’s design choices contributed to the optimization of the layout and stability.”
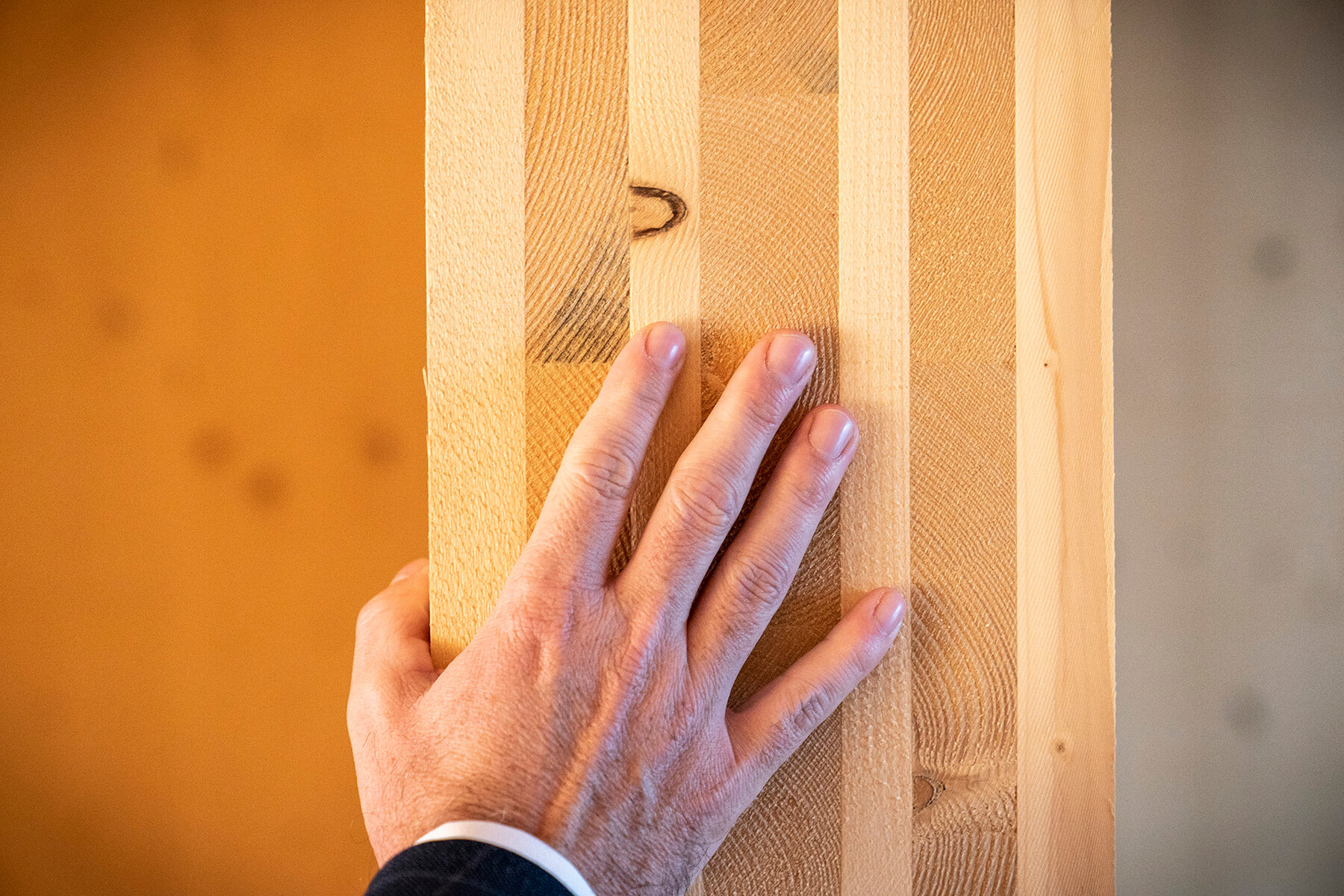
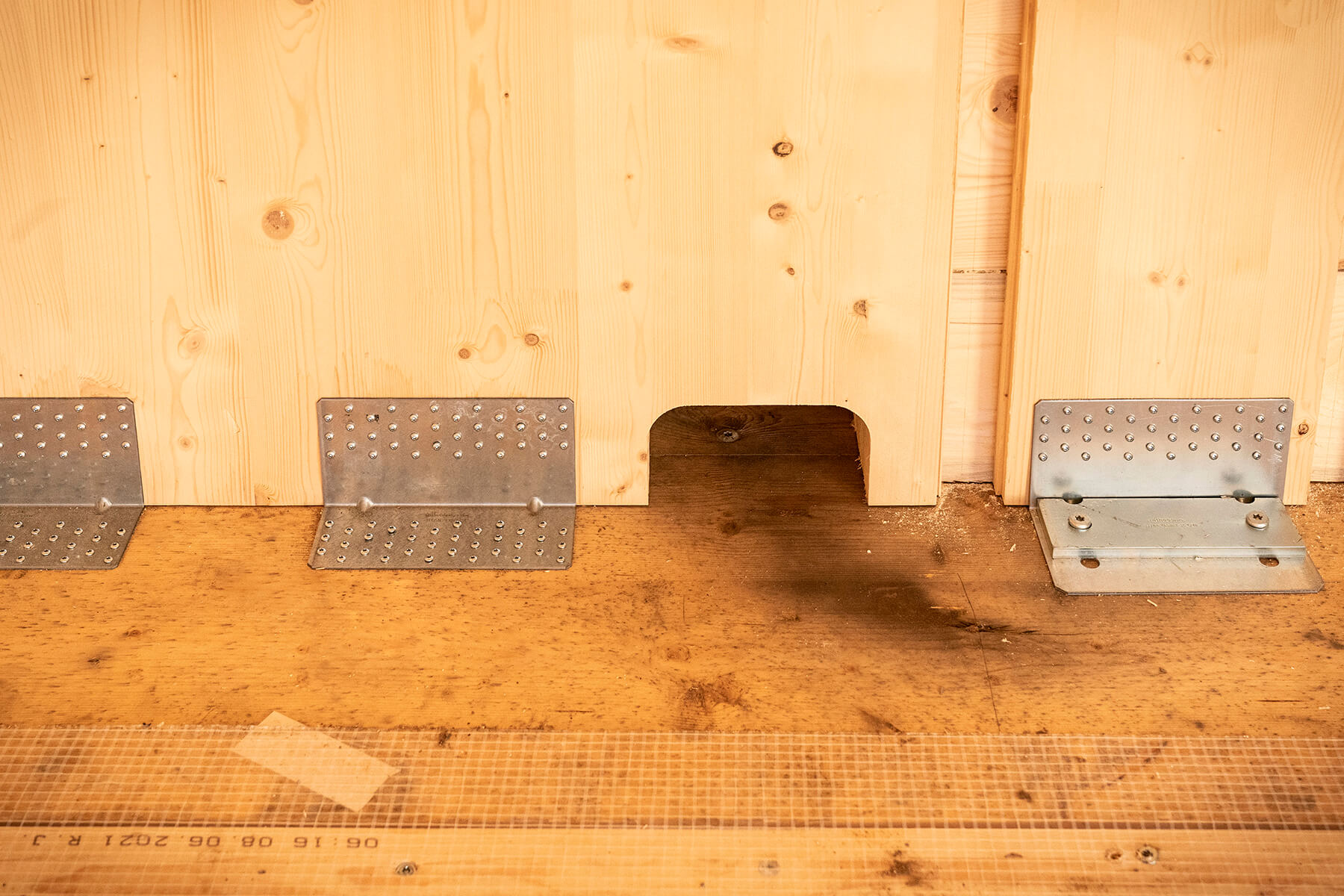
“The partition walls between the homes consist of two layers of five CLT panels with a cavity in between. The structural walls are made of seven layers of CLT. Where it’s not necessary, the walls have been made thinner. Throughout the process, we always considered fire safety and sound insulation. It has been quite a journey of discovery. For example, make sure not to place the electrical outlets of neighboring homes in the exact same spot on the wooden walls, as this creates sound leaks. The beauty of CLT is that it can be prefabricated in the factory. The walls and floors arrive at the construction site, ready to go, on a truck. You might think this limits your choices, but nothing could be further from the truth. There are plenty of options, but homeowners need to make their decisions earlier in the process. These are expectations that need to be managed properly.”
“If you think sustainably, you also have to act sustainably,” Joost continues. “You shouldn’t add things later that aren’t actually sustainable, even if this sometimes conflicts with practicality and feasibility. Some spans were so large that they could hardly be supported by beams in the CLT walls. The beams would then become massive. That’s something you want to avoid. We managed to minimize the number of steel beams. I’m very proud of that, and MKA was always very critical in evaluating this. One lesson we learned is that much can be done with wood, but you must always consider the living quality and stability. This also applies to the finishing of the closed facades, which are made from compressed bamboo slats. These have been thermally modified and, therefore, do not require any treatment. The material also weathers naturally. The choice for closed facade sections was a smart design decision. As a result, we don’t need to make the facade additionally fireproof later, and there are fewer on-site operations required.”
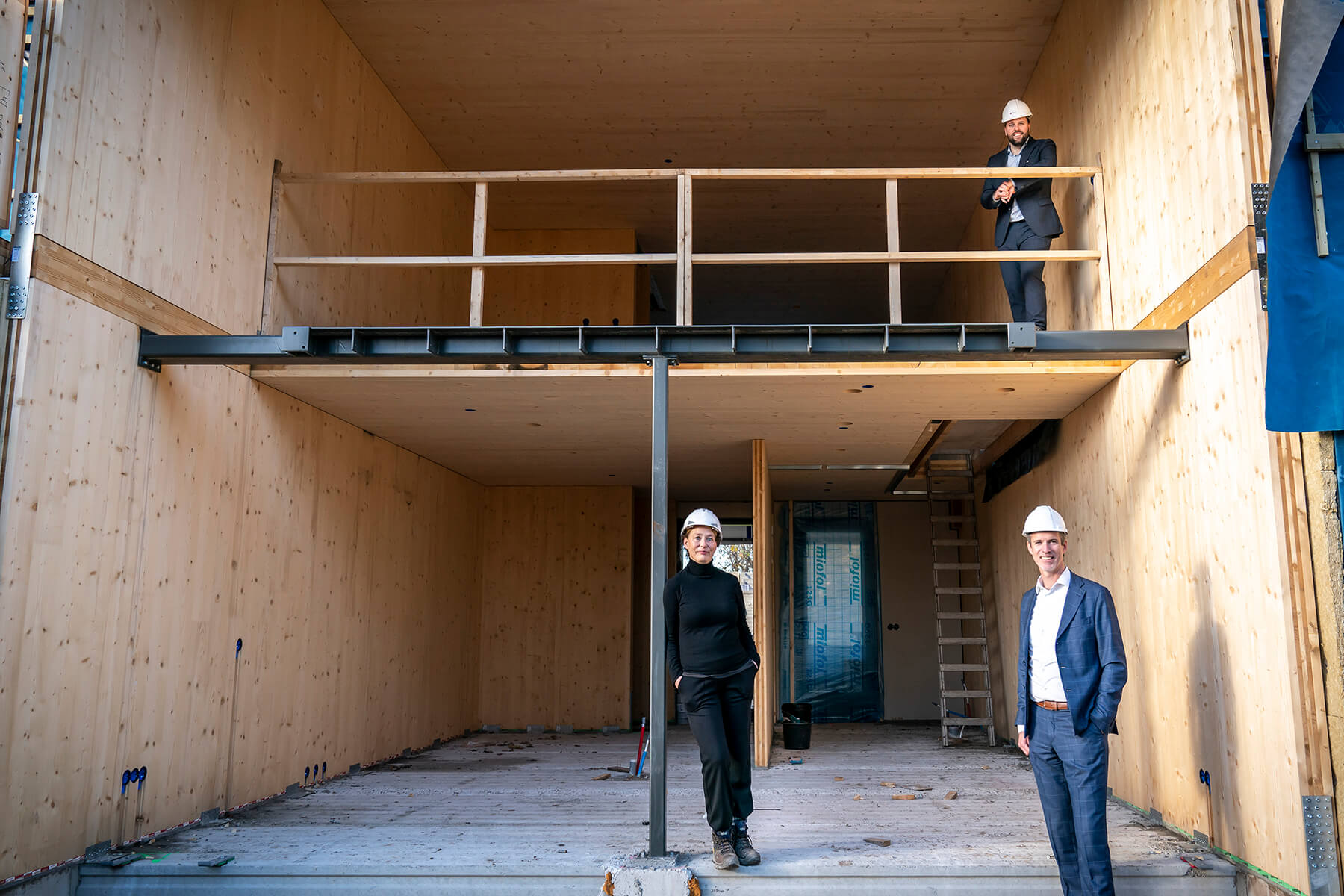
From Vision to Reality
As an architect, Mai was able to let her creativity run free in Bosrijk. “This project is the evolution of the research into wooden homes that our office has been working on for years. From wooden villas in the dunes to wooden mixed-use buildings in Amsterdam like Poppies and Robin Wood. We now also advise the municipality of Amsterdam on the development of an entire wooden residential neighborhood near the Nelson Mandelapark. The fact that Bosrijk is now under construction is the result of an intensive design process. Building wooden homes in combination with flexibility and a bold design doesn’t happen overnight. In the beginning, you have all kinds of dream images and fantasies, but along the way, you have to get practical. It must be feasible and buildable, and at the same time, you want to hold on to a unique design. The decision, for example, to bring in the expertise of Ban Bouw in the field of circular construction methods was a very good one. You know the quality will hold up. Together as a team with the municipality of Eindhoven, we made our dream a reality.”
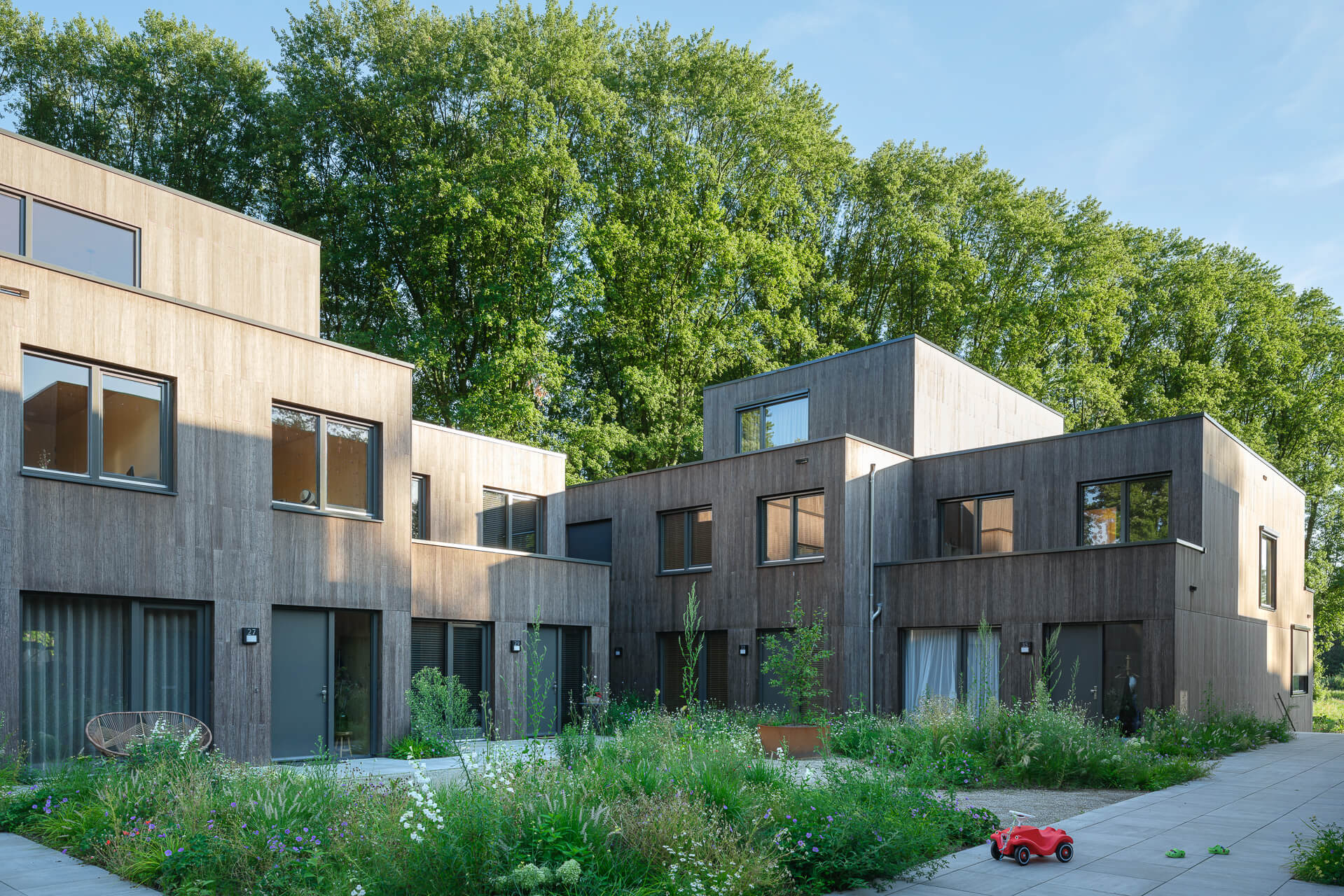
Different approach
According to Ruud, selling wooden homes requires a different approach than selling conventional brick houses. “The design of Bosrijk appeals greatly to buyers, and they make a very conscious choice for it. The shorter construction time is a pleasant bonus for buyers, but it’s not the deciding factor. At the same time, there are also many questions. That’s why we invite buyers to workshops. How do you furnish a home with fully wooden walls and ceilings? What does it mean to live in a wooden house? You need to inspire people to let the wood be. This was greatly appreciated, and as a result, people fell even more in love with their homes.
For example, people asked about the warranty on the wooden structure. I found that surprising because I’ve never been asked that for a house made of brick and concrete. By creating a mockup of the wooden structure, people could see, smell, touch, and experience it for themselves. You really have to appeal to their emotions. How does fire safety, sound insulation, and the indoor climate work? Explain how you build with wood and how thick a wooden wall or floor is. And not just at the beginning of the process, but all the way through to the interior design. Interior designers assist our buyers with questions about how to furnish a wooden home. Not everyone immediately sees the possibilities of a cool wooden house. A bit more persuasion is needed because wooden homes are not yet common in the Netherlands.”
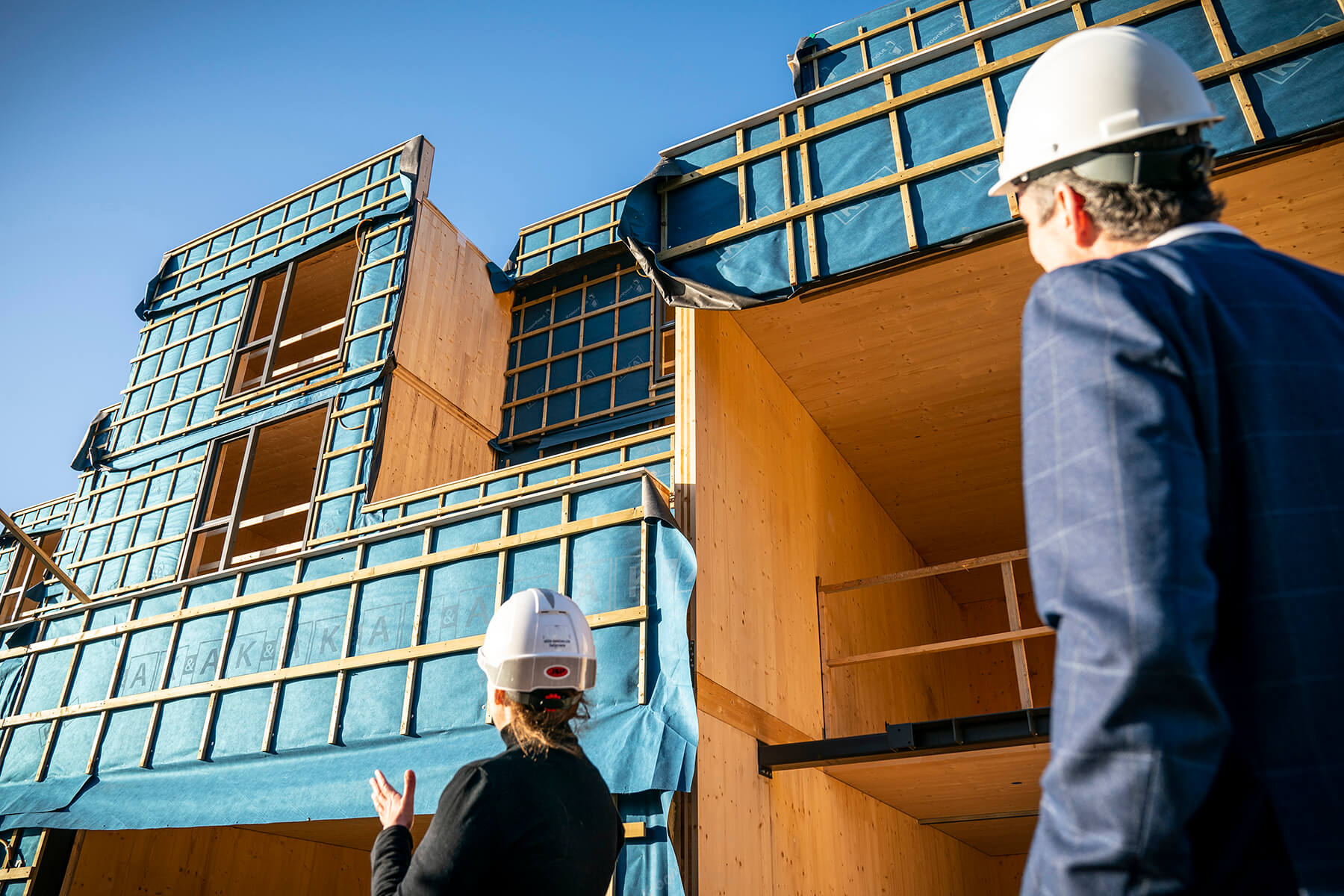
Community Comes to Life
“Designing and building a wooden structure is one thing, but creating a natural environment for a sustainable community is a broader challenge,” says Joost. “These are special homes that appeal to a specific target group. The community aspect is unique. The homes don’t have individual gardens, but they do have spacious private terraces that open up to a public nature area. The terraces are separated by hedges and shrubs, which provide privacy. Here, you have a much larger garden than in a row house, but you share it with the community. Society needs more social interaction and a sense of community, with shared amenities like a neighborhood greenhouse. You share facilities and come together for a drink or a chat. Combine that with unique architecture, and you have something truly different from the typical two-story house with a gable roof.”
Ruud notes that buyers are not only very happy with their homes, but also that they are made of wood. “They share that pride with us. They are ambassadors of the wooden revolution that is currently underway.”